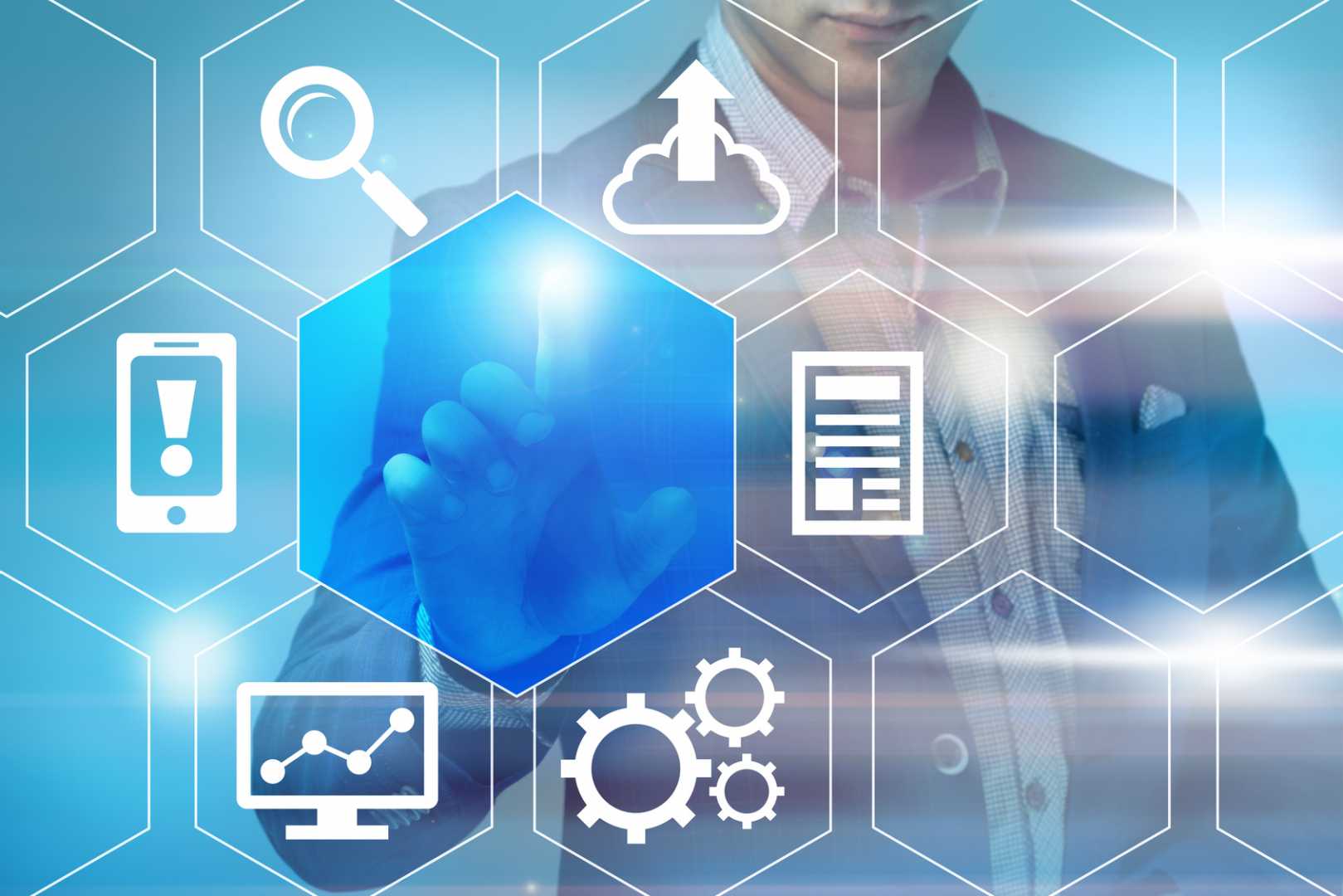
Stamping manufacturing has drastically changed over the years, and technology has played a critical role in improving the precision, efficiency, and outcomes within this industry. The manufacturing sector of the United States has steadily grown over the years with no sign of slowing down, and stamping manufacturing is now critical for many major trades such as the automotive, consumer appliance, and aerospace industries. These are a few aspects of technology that have transformed the stamping manufacturing process:
Automated Production Line
The utilization of automated production lines has been a game-changer in the manufacturing world. By creating production lines comprised of multiple workstations operating in tandem with limited worker interaction, machinery can be programmed and customized for precision with a lower risk to workers. The other benefit of these automated production lines is that while each machine in the line works in tandem, each is independently programmed and can be debugged separately, resulting in a higher level of quality control.
Advanced Simulation Software
Advanced simulation software has allowed stamping manufacturers to simulate each step in the stamping process, from die face design to blank shape and size calculations. Utilizing this software to adjust and develop designs and profiles, as opposed to resorting to trial and error, results in a more time-efficient and streamlined manufacturing process with reduced costs.
Quality Control
Quality control monitoring has been a major technological advance that has improved the efficacy of outcomes for stamping manufacturers in recent years. Statistical control systems and sensors are now able to monitor manufacturing in real time to constantly oversee production and processes, alerting manufacturers to any potential defects or flaws in products. Other technological advances that have greatly benefited quality control in the stamping manufacturing industry include 3D tool design and simulation to plan for quality control from the get-go and proactively identify potential design flaws. These types of quality control technologies have made stamping manufacturers reduce costs and labor related to recalls and defective products, increasing productivity in the long run.
With the long history of Bopp Busch, we have seen many advancements in technology. To be the best supplier partner to our customers, we have incorporated many of these processes and equipment over the decades. We have also supplemented our core stamping services with e-coating, toolmaking, general assembly, and design services. To learn more about Bopp Busch and our capabilities, contact us today.